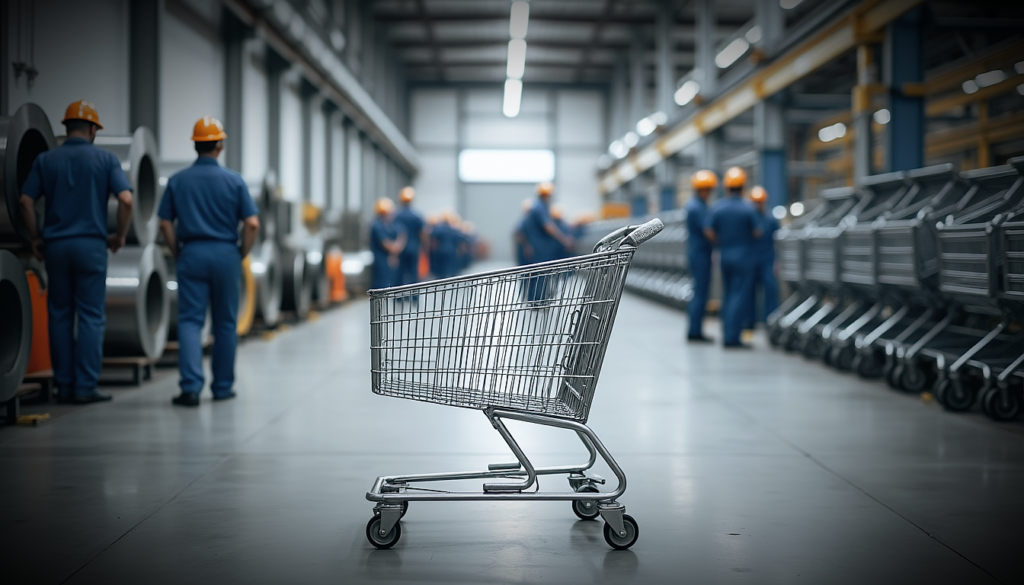
Did you know that the first metal shopping cart rolled into stores in 1937? This innovation became a revolutionary force in the shopping cart manufacturing industry we know today.
A standard shopping cart might look basic, but these engineering marvels pack impressive strength. They can carry up to 600 kg of goods while weighing just 18-25 kg. Modern shopping cart production combines advanced metallurgy with precise engineering. Manufacturers use materials like Q235 steel that provides superior rust resistance and durability.
These carts serve 4-6 years in busy supermarkets when maintained properly, which makes them a vital investment for retailers. The manufacturing process demands specialized knowledge that spans multiple areas. Teams must understand everything from material selection and mechanical bending to welding and electroplating.
This piece walks you through each step of the shopping cart manufacturing process. You’ll learn the quickest way to produce these essential retail tools with economical solutions.
Understanding Shopping Cart Manufacturing Basics
Shopping cart manufacturing requires knowledge of different types, materials, and specialized equipment. Manufacturers must choose between metal or plastic carts at the start since each needs different processes and equipment.
Types of Shopping Carts to Manufacture
The shopping cart industry focuses on two main types: metal and plastic carts. Metal carts made from carbon steel or stainless steel are stronger and last longer when carrying heavy loads. On top of that, manufacturers can make specialty carts like two-tier baskets, rolling handbaskets, and cargo carts that hold up to 440 lbs.
Plastic shopping carts are another option that works well in humid or coastal areas. These carts are made through injection molding, which lets you customize them in up to 10 different colors. Manufacturers also create hybrid models that combine both materials to get the best of both worlds.
Key Materials and Components
The choice of materials shapes how carts are made. Metal cart makers use:
- Carbon steel or stainless steel for the frame and basket
- Zinc electroplating to prevent rust
- Powder coating for longer life
- Rubber or polyurethane for wheel parts
Plastic cart production needs:
- High-quality recycled plastic from consumer and industrial waste
- Special plastic resins for injection molding
- Steel parts for strength
- Polyurethane or TPE materials for wheels
Required Equipment and Facilities
Starting a shopping cart factory needs big investments in specialized machinery. Metal cart production requires:
- Metal processing equipment for bending
- Welding stations
- Zinc electroplating facilities
- Powder coating systems
Plastic cart manufacturing needs:
- Injection molding machines with 2,700-ton clamping force
- Special molds that weigh up to 15 tons
- Cooling systems to solidify parts
- Assembly stations
The factory must have separate zones for different operations. Metal cart production needs dedicated spaces for cutting, bending, welding, and finishing. Plastic cart manufacturing requires areas for material prep, injection molding, cooling, and assembly.
Quality control equipment plays a vital role in both types of manufacturing. Testing facilities check load capacities from 90 to 275 lbs. The manufacturers need special tools to measure structural strength, check wheel alignment, and ensure proper assembly.
Storage space for materials and finished products matters just as much. The facility should have separate areas for:
- Raw material storage (metals, plastics, parts)
- Work-in-progress inventory
- Finished product warehousing
- Quality control testing
Modern cart manufacturing now includes automated systems and precise machinery. The latest facilities use:
- Automated machining centers
- Precision cutting equipment
- Robotic welding systems
- Computer-controlled injection molding machines
The factory layout should optimize workflow. Manufacturers arrange equipment and workstations to create a smooth flow from raw materials to final assembly. This setup reduces material handling time and makes production more efficient.
Setting Up Your Production Line
A successful shopping cart manufacturing operation needs a solid production line setup. Smart facility planning will streamline processes and create smooth operations from raw materials to final assembly.
Factory Layout Planning
Creating the best manufacturing layout needs smart space usage and material flow planning. Manufacturers must first create detailed spaghetti diagrams that show how materials and work-in-process parts move between manufacturing cells. This helps spot potential bottlenecks and improves production flow.
Smart manufacturers set up temporary mock layouts before making final decisions. They test these layouts with real carts to find tight spots or safety issues. This early testing is a great way to get avoid changes that might get pricey later.
The Systematic Layout Planning (SLP) method gives a well-laid-out approach to organizing production spaces. This method focuses on:
- Smart machine and equipment placement
- Efficient material flow patterns
- Logical production sequences
- Worker movement coordination
The facility layout must account for:
- Warehouse and inventory storage
- Kitting and component preparation areas
- Dedicated work cells
- Production zones
- Quality control stations
Equipment Installation
Modern shopping cart production depends on automated systems that deliver consistency and efficiency. A well-configured production line can make up to 600 frames per day using twin-head benders. Precise equipment installation plays a vital role in keeping these high production rates.
The setup starts with positioning core manufacturing equipment:
- Automated tube bending cells
- Punching machines
- Welding stations
- Surface treatment facilities
Automated bending cells are the heart of the production line. These systems need:
- Bundle retrieval mechanisms
- Punching machine integration
- Weld seam detection capabilities
- Precise tube orientation controls
- Automated loading/unloading systems
Manufacturers should use servo-driven technology in their bending equipment to get optimal performance. This closed-loop control system gives precise and consistent results that ensure dimensional accuracy in all production runs.
Proper machine spacing is key during equipment installation. Good spacing allows smooth material flow and prevents bottlenecks. The layout must also fit frequent tooling changes since modern facilities handle up to 10 changeovers daily.
Surface treatment equipment needs designated zones for:
- Zinc electroplating processes
- Powder coating applications
- Curing and drying operations
The final assembly line setup must support smooth component integration. This means installing:
- Frame assembly stations
- Basket attachment points
- Wheel mounting areas
- Quality testing equipment
Manufacturers should think over modular and expandable equipment solutions to keep production flexible. This lets them quickly modify the setup for different cart models or production volumes. The layout should also have enough space for material staging and finished product storage to keep work flowing smoothly.
Good equipment installation also needs safety features and ergonomic design. This includes:
- Emergency stop systems
- Safety barriers
- Proper ventilation
- Adequate lighting
- Ergonomic workstations
Material Selection and Preparation
Quality raw materials are the life-blood of successful shopping cart manufacturing. Material quality directly impacts how durable and long-lasting the final product will be.
Choosing Quality Raw Materials
Q235 SPCC steel is the top choice for metal shopping cart manufacturers. This grade of steel has exceptional ductility that allows quick construction through prefabrication processes. The steel’s reliable nature helps carts maintain their structure even with heavy loads.
High-Density Polypropylene Plastic (HDPP) is the main material used in plastic cart production. This material melts between 200-250 degrees Celsius with a 1% shrinkage rate. HDPP’s semi-crystalline structure provides great flexural strength and resists chemicals and acids well.
Today’s manufacturers use more recycled materials in their production. They process post-consumer and post-industrial waste carefully to create environmentally responsible shopping carts. This approach reduces landfill waste and creates a more sustainable manufacturing process.
Material Testing Procedures
A complete material testing process ensures shopping carts are reliable and last longer. Manufacturers run several key tests:
- Salt Spray Testing: This environmental test simulates coastal conditions to review rust resistance. Manufacturers spray artificial salt solutions on cart components to check how well they resist corrosion.
- UV Resistance Testing: Materials undergo intense ultraviolet light exposure for 72 hours to simulate accelerated aging. This test matters most for carts headed to tropical regions.
- Load Testing: Components go through weight assessments to verify their load capacity. Tests check both static and dynamic performance and analyze caster movement.
Manufacturers must also meet regional and international standards. Testing labs conduct specialized assessments for chemical, mechanical, technological, corrosive, thermal, and wear factors. These detailed evaluations reduce risks and prevent product failures throughout the cart’s life.
Storage and Handling Guidelines
Good storage and handling keeps materials in top condition during manufacturing. Materials need dedicated storage areas with controlled conditions to stay clean and undamaged.
Key storage guidelines include:
- Keep materials in temperature-controlled environments at 73±9°F (23±5°C) for at least 48 hours before use
- Shield from moisture and direct sunlight
- Use proper ventilation systems
- Organize based on production schedules
- Use clear inventory tracking systems
Material handling requires careful attention. Manufacturers should rotate stock using First-In-First-Out (FIFO), so older materials get used first. The right lifting and transportation methods help maintain quality from storage to production.
Metal components should stay away from water sources or tarps that might trap moisture and damage the material. Plastic materials need protection from extreme temperatures that could change their molecular structure.
Quality checks start when materials arrive. Inspectors match material specs with supplier documents, checking dimensions, chemical makeup, and physical properties. First-article inspections catch problems before materials enter production.
Records of material batches must include supplier details, test results, and any unusual findings. These documents are a great way to track materials and improve selection processes.
Metal Cart Manufacturing Process
Shopping cart manufacturers today rely on precise metal fabrication techniques to turn raw steel into long-lasting retail essentials. Each stage of the process just needs careful attention, from the first cut to the final surface treatment.
Cutting and Shaping Metal Parts
The manufacturing experience starts when workers cut steel tubes to specific lengths and bend them strategically. Modern twin-head benders help manufacturers make up to 600 frames daily. These machines have special weld seam detectors that stop splits by arranging the seam with the neutral axis instead of the bend axis.
Manufacturers must maintain these elements to get the best bending results:
- Right clearance between bending parts
- Steady hydraulic fluid temperature
- Exact tube orientation controls
- Precise seam detection systems
Building the basket takes three main steps. Workers cut wires to length and space them correctly. They use resistance welding to join these wires. Special equipment then applies about 20 tons of force to shape the assembly into a basket.
Welding and Assembly
The welding phase combines precision and automation after shaping individual parts. Robotic welding systems create consistent joint quality throughout the cart structure. Each cart just needs about 150 steel pieces, and every component must sit in the exact position.
Silicon bronze welding has become the quickest way to assemble carts. This method works best with:
- Pulse settings at 30% on-time
- Background current at 30%
- One pulse per second rate
Assembly follows a clear order where workers create sub-assemblies before final integration. Jigs and fixtures are the foundations of faster assembly times. Skilled workers can finish frame assembly in about 14.5 minutes when they use proper jigging techniques.
Surface Treatment and Finishing
Surface treatment plays a crucial role in making carts last longer. Most manufacturers use an 11-stage electrocoat dip-tank finishing system. This complete process has:
- Multi-tank cleaning
- Zinc phosphate precoating
- Acrylic electrodeposition
- Oven curing
Two coat powder coating systems work best, giving superior salt spray resistance of minimum 1,500 hours. Manufacturers can pick from several pretreatment options before powder coating:
- Chromate application
- Zinc phosphate treatment
- Manganese phosphate coating
Some facilities boost durability with DK-SEAL, a specialized finishing process that uses:
- Zirconium pre-treatment
- Infrared drying
- HD thermoset coating
- SLIP antifriction coating
- High-temperature baking
ASTM standards guide rigorous testing of the final surface treatment to check adhesion, durability, cure quality, and coating thickness. These treatments shield against water exposure, humidity, salt, UV rays, and extreme temperature changes.
Good surface preparation makes coating successful. Manufacturers avoid putting powder coating directly on zinc plating without pretreatment because it won’t stick. They often pick automotive-grade finishing systems that protect even hard-to-reach areas and joints.
Plastic Cart Production Steps
Plastic shopping cart manufacturing is different from metal cart production. The process uses specialized injection molding techniques and precise cooling steps to create durable retail equipment. This unique method needs careful attention to material preparation and temperature control throughout production.
Injection Molding Process
The production of plastic carts starts when granular polypropylene (PP) and polyamide (nylon) materials are prepared. These materials go into the injection molding machine through a special funnel system and into the injection barrel. Heat elements then melt these granules into liquid form.
The barrel’s rotating screw has two important jobs:
- It moves the melted plastic forward
- It pushes the material into the mold cavity
Large parts like shopping cart baskets need injection molding machines with strong clamping force. These machines apply up to 2,700 tons of pressure to keep the mold closed and stop material from leaking. This massive pressure is needed because it:
- Keeps the mold tightly closed
- Stops parts from getting damaged
- Protects expensive mold parts
- Makes sure each part meets quality standards
The molding cycle begins right after the mold closes. Robotic systems help move smoothly between cycles and collect finished parts while new ones start production.
Cooling and Solidification
The cooling phase takes up about 70-80% of the total molding cycle time. This step determines how fast parts can be made and their final quality. Several systems work together during cooling:
Water cooling systems are common but need:
- Perfect pipeline seals
- Clear upper and lower water pipes
- Regular maintenance to avoid waste
Air cooling gives some better options:
- No need for tight pipeline seals
- Less resource waste
- Works with mold temperatures above 100°C
- Cooling rates can be adjusted by controlling gas flow
Wall thickness mainly determines cooling time – thicker parts need more time to cool. The cooling time usually relates to:
- The square of how thick the part is
- The 1.6th power of the largest gate diameter
The mold material choice affects cooling speed. Cooling works better when:
- Water pipes are closer to mold cavities
- Pipes are wider
- There are more cooling channels
Turbulent water flow in cooling channels removes heat better through convection. The cooling liquid’s features also matter:
- Lower viscosity makes cooling better
- Better heat conductivity improves heat transfer
- Colder liquid speeds up the process
The cooling system must keep temperature even throughout the mold. Even temperatures prevent problems like:
- Shrinkage marks
- Warping
- Uneven hardening
After proper cooling, the movable mold part opens to release the finished piece. This careful process makes sure each plastic cart part meets exact specifications while keeping production moving quickly.
Assembly Line Operations
Shopping cart manufacturing success depends on how well the assembly line runs. Manufacturers combine components and check quality at every step to build carts that meet exact specifications.
Component Assembly Sequence
Automated systems start by pulling tubes from material bundles. These machines feed components into punchers that create holes needed for later assembly. Smart detection systems spot weld seams and position tubes correctly before bending.
Today’s assembly lines use twin-head benders that make matching parts with amazing accuracy. These automated cells work on several tasks at once:
- Getting materials from bundles
- Positioning components
- Making precise holes
- Loading and unloading parts
Basket building happens in three steps. Teams arrange cut wires in specific patterns. Resistance welding joins these parts together. Special equipment then applies approximately 20 tons of force to shape everything into its final form.
Mounting bracket units are vital to frame assembly. Each unit has:
- A plate with two parts
- Flanges set apart
- Holes for caster pins
- One-piece design
Primary and secondary baskets need exact positioning. The main basket extends forward while the secondary one sits lower and toward the back. This setup saves space and makes shopping easier.
Quality Checks During Assembly
Quality checks happen throughout assembly. Manufacturers use complete testing methods to review every part of cart construction:
- Adhesive Testing
- 3M tape checks coating grip
- Paint, plating, and screen print tests
- Stability Assessment
- Tests on 15-degree slopes
- Checks for base wobble
- Wheel alignment tests
- Component Testing
- Pull tests on power cords (35-pound weight for 1 minute)
- Hi-pot tests at 1500V
- Ground checks for class I items
- Functional Verification
- Barcode scanner tests
- Accessory checks
- Internal part inspection
Manufacturers keep detailed records of:
- Material batch numbers
- Test results
- Quality outcomes
- Assembly steps
Modern laser-based seam detectors ensure parts line up perfectly. These systems work better than old camera systems that looked for color differences between materials. They cost just one-tenth as much.
Production lines must switch between products quickly. Advanced factories handle up to 10 different frames and handles each day. This takes:
- Quick tool changes
- Smart part organization
- Fast-swap fixtures
- Perfect alignment steps
Surface treatment checks are vital during assembly. Quality teams run salt spray tests to ensure finishes last through 1,500 hours of exposure. They also check wheel installation to make sure all four wheels touch the ground evenly, which prevents wobbling.
Final inspection looks at:
- Structure strength
- Part alignment
- Surface quality
- Smooth operation
- Safety standards
Quality Control Measures
Quality control plays a vital role in shopping cart manufacturing to ensure durability and keep customers happy. A detailed quality assurance program has multiple testing phases and strategies to prevent defects.
Testing Standards and Procedures
Quality control starts when materials arrive at the factory and continues through each manufacturing step. Manufacturers follow detailed guidelines with clear criteria for every product component. These guidelines spell out testing procedures for:
Surface Treatment Evaluation:
- Salt spray resistance testing for minimum 1,500 hours exposure
- UV resistance assessment through 72-hour intense light exposure
- 3M tape adhesive testing for coating adherence
- Load capacity verification ranging from 90 to 275 pounds
- Stability assessment on 15-degree inclined surfaces
- Pull tests using 35-pound weights for one minute duration
Shopping carts must meet specific requirements to keep children safe. Tests verify:
- Child restraint system durability
- Passive crotch restraint functionality
- Child-resistant buckle operation
- Permanent attachment of restraint systems
Modern factories use automated inspection tools and IoT devices to monitor production in real-time. These systems track key metrics like first pass yield – calculating quality units against total production volume. Regular audits help ensure the standards stay consistent.
Common Defects to Watch For
Quality teams must watch for specific defects that often show up during production. Data analysis shows six main types of defects:
- Spot welding issues (53% of total defects)
- Non-standard assembly problems (30%)
- Coarse welding (6%)
- Sharp cutting edges (4%)
- Uneven surfaces (3%)
- Spot weld spread (2%)
Manufacturers prevent these defects through multi-stage inspections. Quality specialists check:
- Wheel alignment and stability
- Frame structural integrity
- Surface finish consistency
- Component assembly precision
Good maintenance helps prevent defects. Quality teams look for:
- Wobbly wheels caused by caster flutter
- Broken wire frames requiring immediate welding
- Damaged child seat belts necessitating replacement
- Cracked child seats affecting safety
Factories must keep detailed records of all quality control measures. Records show:
- Inspection results at each production stage
- Equipment maintenance schedules
- Material batch tracking information
- Defect occurrence patterns
Modern factories use ERP systems to track quality control effectively. These systems show production stages in real-time and help quickly spot and fix quality issues. Customer feedback and product returns help identify potential quality problems before they hurt revenue.
Packaging and Storage
Shopping carts need proper packaging and storage methods to protect them during their trip from production to retail stores. The manufacturing process’s final stage needs careful attention to shield these valuable assets from damage and environmental factors.
Protective Packaging Methods
Cart integrity during transit relies on strategic packaging solutions that combine multiple protective elements. Manufacturers employ specialized void fillers and custom inserts to eliminate empty spaces in shipping containers. These fillers prevent movement and provide cushioning against sudden impacts.
Manufacturers use a complete packaging approach that has:
- Primary Protection Layer
- Water-based adhesives to prevent slippage
- Cold-applied solutions that leave no residue
- FDA-approved ingredients for safe handling
- Secondary Safeguards
- Multi-layer film technology for moisture control
- Edge protection made from recycled laminated paper
- Commingled paper and plastic materials
Advanced stretch hood technology stands out as a premier solution in cart protection. This innovative system provides ’10-sided’ waterproof protection through five exterior and five interior surfaces. The specialized film keeps barcodes readable and resists tears and punctures as bags stretch over corrugated loads.
Material selection must account for environmental impact. Modern facilities now use green solutions that boost brand recognition and reduce carbon footprints. These eco-friendly options have:
- Foam packaging for shock absorption
- Lightweight bubble wrap containing 80% recycled content
- Curbside recyclable embossed paper
Storage needs equal attention to protective measures. Facilities use automated storage and retrieval systems (AS/RS) to streamline space usage. These cart-based systems work best in:
- Space-limited environments
- Cold storage conditions
- High-volume inventory management
Manufacturers use modular and stackable packaging designs to save storage space. This approach offers several benefits:
- Lower shipping costs
- Better warehouse space use
- Better retail shelf presentation
- Easier inventory management
Quality corrugated boxes protect carts effectively. The global market value should reach USD 294.00 billion by 2023. These boxes provide key advantages:
- Better stacking capability
- Improved storage optimization
- Reliable product security
Materials need controlled environmental conditions at 73±9°F (23±5°C) for at least 48 hours before processing. Good ventilation systems prevent moisture buildup that could damage cart integrity.
Storage facilities use specialized corral systems built for cart protection. These systems come with:
- Weather-resistant coverings
- Secure locking mechanisms
- Well-planned storage arrangements
- Quick retrieval systems
Manufacturers keep their shopping carts in pristine condition from production through delivery by using these packaging and storage solutions carefully. Advanced protective materials, strategic storage systems, and environmental controls work together to shield against damage or deterioration.
Conclusion
Shopping cart manufacturing requires meticulous attention to detail at every production step. Today’s facilities blend advanced metallurgy with automated systems and strict quality control. This combination creates lasting retail assets that businesses can use for years.
Quality shopping cart production depends on premium materials, strict manufacturing standards and extensive testing. Manufacturers of metal and plastic carts must prioritize durability, safety and consistent quality in their product lines.
Modern techniques like twin-head benders and automated welding systems help facilities produce carts quickly without quality issues. The right materials and surface treatments, combined with this technology, help carts last longer in retail environments of all types.
Quality control plays a vital role throughout the production process. Each stage needs thorough testing. Manufacturers track common defects and keep detailed records of all quality measures.
JY Shopfitting creates custom shopping cart solutions that match specific retail needs – contact John to get a detailed product catalog. A steadfast dedication to quality drives successful cart manufacturing, from the original material selection to final packaging and storage.
FAQs
Q1. What materials are commonly used to manufacture shopping carts? Shopping carts are typically made from metal (such as carbon steel or stainless steel) or plastic (like high-density polypropylene). Metal carts offer superior strength and durability, while plastic carts are suitable for humid environments. Some manufacturers also produce hybrid models combining both materials.
Q2. How long does a typical shopping cart last in a retail environment? With proper maintenance, shopping carts can serve 4-6 years in high-volume supermarkets. However, their lifespan can vary depending on usage, maintenance, and the quality of materials and manufacturing processes used.
Q3. What are the key steps in the shopping cart manufacturing process? The manufacturing process includes material selection, cutting and shaping components, welding and assembly, surface treatment and finishing, quality control checks, and packaging. For plastic carts, the process involves injection molding and cooling steps.
Q4. How do manufacturers ensure the quality and safety of shopping carts? Manufacturers implement rigorous quality control measures throughout the production process. This includes material testing, structural integrity assessments, surface treatment evaluations, and functional verification. They also conduct stability tests and ensure compliance with safety standards, especially for child seats.
Q5. What innovations are being introduced in shopping cart manufacturing? Recent innovations include the use of automated systems for increased efficiency, implementation of eco-friendly materials and processes, development of smart carts with digital features, and advancements in surface treatments for enhanced durability and corrosion resistance.