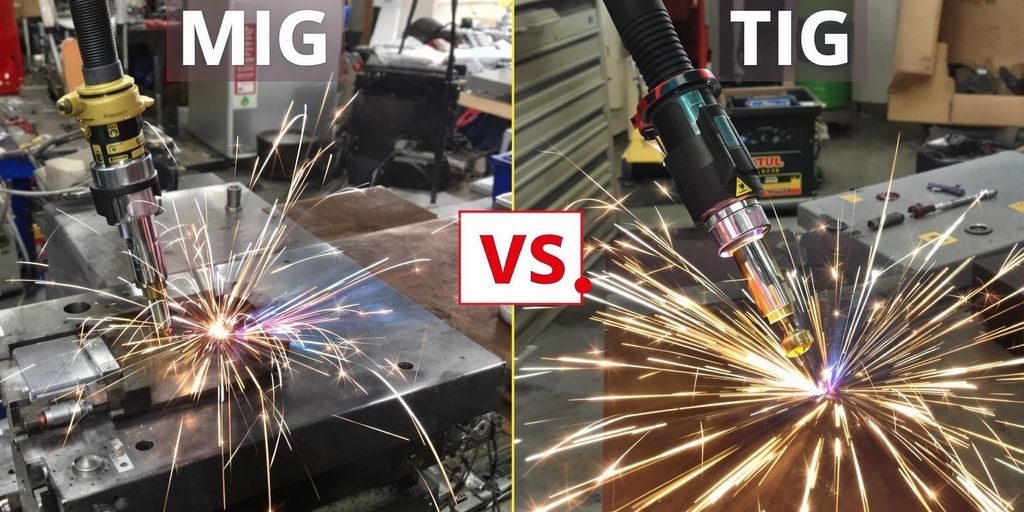
Trying to decide between MIG and TIG welding? It’s not always an easy call. Both methods have their own pros and cons, and the right choice often depends on the job at hand. Whether you’re tackling a DIY project or working on a professional job site, knowing the ins and outs of these techniques can save you time, money, and frustration. Let’s break down the difference between TIG and MIG welding so you can pick the best option for your needs.
Key Takeaways
- MIG welding is faster and easier to learn, making it great for beginners and high-production tasks.
- TIG welding offers more precision and cleaner welds, ideal for intricate or high-quality projects.
- When comparing a MIG welder vs TIG, MIG is often more cost-effective upfront, while TIG can require a larger initial investment.
- Both methods have unique safety and environmental considerations, like fume control and energy use.
- The choice between TIG vs MIG welding depends on your project’s material, budget, and skill level.
Understanding MIG Welding
How MIG Welding Works
MIG welding, short for Metal Inert Gas welding, is a process where a continuous wire electrode is fed through a welding torch. The wire melts as it contacts the base material, creating a strong weld bead between the metals. A shielding gas, typically argon or a mix of argon and CO2, is used to protect the weld from atmospheric contamination. This method is especially popular because it’s straightforward, even for beginners, and works well on metals like steel, aluminum, and stainless steel.
Advantages of MIG Welding
- Ease of Use: MIG welding is beginner-friendly, with a relatively short learning curve compared to other methods.
- Speed and Efficiency: Ideal for large-scale projects, this method allows for continuous welding without frequent stops.
- Versatility: Works on a variety of metals and thicknesses, making it suitable for both industrial and DIY applications.
- Clean Welds: Since no flux is used, there’s minimal cleanup required, and the finished welds are smooth and polished.
Common Applications of MIG Welding
- Automotive Repairs: Perfect for fixing car panels and frames due to its precision and speed.
- Construction Projects: Used in building frameworks and other structural components.
- DIY and Hobby Projects: A go-to for home enthusiasts working on everything from metal furniture to custom art pieces.
MIG welding is often the first choice for beginners and professionals alike, thanks to its balance of simplicity and capability. When considering MIG welding vs TIG welding, MIG is most effective when working on thicker materials or when high welding productivity is required.
Exploring TIG Welding
How TIG Welding Works
TIG welding, also known as Gas Tungsten Arc Welding (GTAW), uses a non-consumable tungsten electrode to produce the weld. An electric arc forms between the tungsten electrode and the metal workpiece, generating intense heat that melts the base material. What sets TIG welding apart is its precision and the ability to create high-quality welds with excellent weld penetration. Unlike MIG welding, the tungsten electrode doesn’t melt; it stays intact throughout the process. Here’s how the process works:
- The workpiece is cleaned to remove contaminants and oxides.
- The tungsten electrode is positioned close to the metal surface.
- An inert shielding gas, often argon or helium, is released to protect the weld from contamination.
- The welder manually feeds filler metal into the weld pool, if needed.
A foot pedal is often used to control the heat, allowing for refined adjustments during the welding process. This makes TIG welding ideal for applications requiring a clean, polished finish and superior welding precision.
Advantages of TIG Welding
TIG welding offers several benefits that make it a preferred choice for specific projects:
- Precision: The technique allows for detailed and accurate welds, perfect for intricate work.
- Clean Finish: Minimal spatter and slag mean less post-weld cleanup.
- Versatility: TIG welding works well with a wide range of metals, including aluminum, stainless steel, and titanium.
These advantages make it popular in industries like aerospace, automotive, and art installations where aesthetics and durability are key.
Common Applications of TIG Welding
TIG welding is widely used in scenarios where precision and appearance matter. Some common applications include:
- Fabricating stainless steel kitchen equipment.
- Creating custom automotive parts.
- Repairing delicate components like bicycle frames or sculptures.
TIG welding is often the go-to method when the final appearance of the weld is as important as its strength. Its ability to produce smooth, visually appealing welds makes it invaluable for high-quality projects. For more insights into TIG welding techniques and applications, check out explore TIG welding.
Key Differences Between MIG and TIG Welding
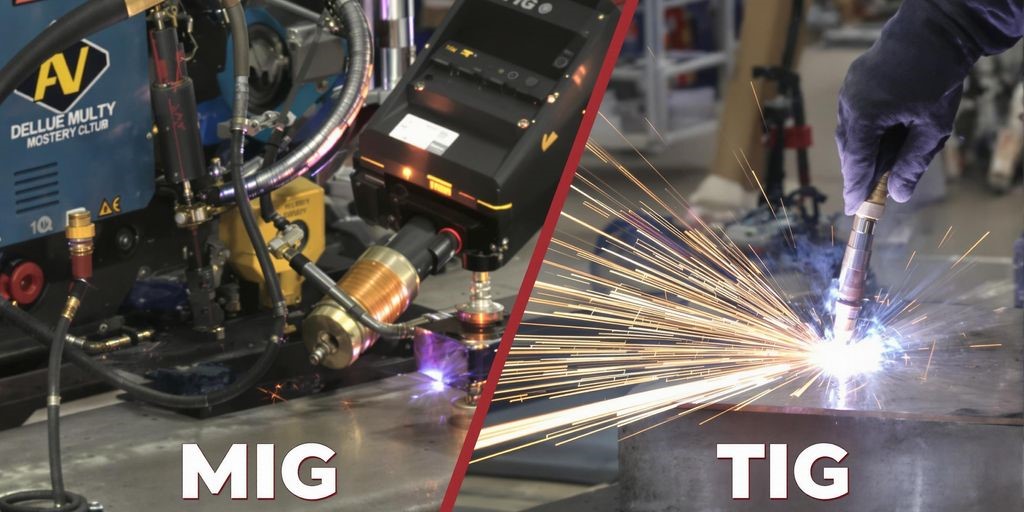
When comparing MIG weld vs TIG weld, it’s important to understand their fundamental differences. MIG welding uses a consumable wire electrode that doubles as filler material, which is fed continuously through the welding gun. In contrast, TIG welding employs a non-consumable tungsten electrode, with filler material added manually if needed. This distinction makes TIG welding more precise but also more demanding in terms of skill. The tungsten electrode in TIG welding remains intact, while the MIG electrode melts to form the weld joint.
Speed and Efficiency
When it comes to weld speed, MIG welding takes the lead. It’s faster due to its automated wire feeding system, making it ideal for large-scale or high-volume projects. TIG welding, on the other hand, is slower and more methodical, as it often requires manual feeding of filler material and greater attention to detail. For projects where time is a critical factor, MIG welding is the go-to option.
Precision and Aesthetics
TIG welding is renowned for its precision and the clean, beautiful welds it produces. This makes it the preferred choice for projects where appearance matters, such as decorative metalwork or visible joints. When comparing TIG vs MIG beads, TIG typically results in more aesthetically pleasing welds, which may require less additional finishing. TIG welding also excels with thinner materials, as it reduces the risk of warping or burn-through compared to MIG welding.
Choosing between MIG and TIG welding often comes down to balancing speed and efficiency against precision and appearance. Understanding your project’s specific needs, including material thickness and desired weld strength, will guide you to the right method.
Choosing the Right Welding Method for Your Project
Factors to Consider
Picking between MIG and TIG welding isn’t as simple as flipping a coin. Each method has its own strengths and trade-offs, so your decision should be based on several key factors:
- Material Type: MIG works well with thicker metals, while TIG is ideal for thin, delicate materials like aluminum or stainless steel.
- Project Size: For larger projects requiring speed, MIG is often the better choice. TIG excels in smaller, detail-oriented work.
- Environment: If you’re welding outdoors, MIG’s shielding gas can be a challenge in windy conditions, whereas TIG might perform better indoors where precision is key.
When to Choose MIG Welding
MIG welding shines in projects that demand speed and efficiency. Here’s when it’s the go-to method:
- High-Volume Work: Perfect for production lines or repetitive tasks where welding productivity is crucial.
- Thicker Metals: Handles steel and other heavy materials with ease, providing good weld strength.
- Beginner-Friendly: Easier to learn, making it great for hobbyists or those new to welding.
When to Choose TIG Welding
TIG welding is all about precision and quality. Consider this method in the following cases:
- Artistic or Detailed Work: Ideal for intricate designs or high-quality finishes where weld aesthetics matter.
- Thin Materials: Works well with delicate metals that require a lighter touch and precise welding control.
- Environmentally Conscious Projects: TIG produces fewer fumes and is generally cleaner.
Ultimately, the “right” welding method depends on your specific needs. A good rule of thumb is to evaluate the material, project scale, and your own skill level before committing to a technique. Whether you choose MIG or TIG welding, understanding the difference between MIG and TIG welder capabilities will help you make an informed decision.
Skill Level and Learning Curve
Ease of Learning MIG Welding
MIG welding is often seen as the go-to choice for beginners. Why? Because it’s straightforward. The process uses an automated wire feed, which means you don’t have to juggle too many things at once. This simplicity lets you focus on the basics—like how to hold the welding torch and move it in a steady line. Even if your technique isn’t perfect, MIG welding is forgiving, making it easier to get decent results quickly. If you’re just starting out, this method can help you build confidence without overwhelming you.
Challenges of Mastering TIG Welding
TIG welding, on the other hand, is a whole different beast. It’s not beginner-friendly, and there’s no sugarcoating that. You’ve got to use both hands—one for the torch and another for the filler rod. Plus, you need to keep the weld pool steady, which takes real skill. Precision is the name of the game here, and that means there’s no room for error. The welding difficulty is higher, as it requires more welding control and finesse. It’s a steep learning curve, but for those who stick with it, the payoff is worth it. You’ll be able to create some of the cleanest, most professional-looking welds out there.
Tips for Beginners
- Start with MIG welding to get a feel for the basics.
- Practice regularly to build muscle memory and improve control.
- Don’t rush into TIG welding until you’re comfortable with simpler techniques.
MIG welding is a great entry point, but TIG welding is where you’ll truly test your skills. Take it one step at a time, and don’t be afraid to make mistakes—they’re part of the learning process. Understanding the difference between MIG and TIG welding will help you choose the right path for your skill development.
Cost and Equipment Considerations
When it comes to getting started, MIG welding equipment tends to be more budget-friendly. The machines are widely available, and you can find decent options for a lower price compared to TIG welders. Consumables like wire spools and shielding gas are also relatively affordable. This makes MIG welding a go-to for hobbyists and small-scale projects. However, keep in mind that higher-end MIG setups can still rack up costs, especially if you need advanced features.
Costs Associated with TIG Welding
TIG welding, on the other hand, demands a heftier upfront investment. The equipment is more specialized, and accessories like tungsten electrodes and high-quality shielding gas can add up. Plus, TIG welders often require additional attachments for foot pedals or water coolers. While the precision and clean welds are worth it for many applications, the higher welding costs might be a dealbreaker for some.
Long-Term Maintenance and Consumables
Over time, the costs of maintaining your welding setup can vary significantly. MIG welding might seem cheaper initially, but regular upkeep—like replacing worn-out nozzles, liners, and drive rolls—can eat into your budget. TIG welding, while requiring less frequent consumable replacement, involves meticulous care for the tungsten electrode and other parts. The long-term expenses for either method depend on how often you weld and the materials you work with.
When considering MIG or TIG welding, it’s important to factor in both initial and ongoing costs. While MIG is typically more cost-effective, TIG’s precision and higher deposition rate for certain materials might justify its higher price tag for specific applications.
Environmental and Safety Aspects
Fume and Spatter Control
Welding processes like MIG and TIG can release harmful fumes and spatter that pose risks to both health and the environment. Proper ventilation is critical to reducing exposure to toxic gases and particles. Here are a few tips for managing fumes and spatter effectively:
- Use local exhaust systems to capture fumes directly at the source.
- Keep the workspace free of flammable materials to avoid fire risks from spatter.
- Regularly clean and maintain your equipment to minimize unnecessary emissions.
Always ensure your workspace is equipped with adequate ventilation systems and follow safety guidelines to protect yourself and others, regardless of whether you’re using TIG and MIG welding techniques.
Energy Consumption
Welding machines can be power-hungry, contributing to higher energy bills and environmental strain. While MIG welding typically consumes more power due to its speed and continuous wire feed, TIG welding is more energy-efficient for precision tasks. To reduce energy consumption:
- Use energy-efficient welding machines.
- Turn off equipment when not in use.
- Opt for processes that match the scale and scope of your project.
Safety Gear and Precautions
Protective gear is non-negotiable when it comes to welding safety. From shielding your eyes to preventing burns, the right equipment can make all the difference. Essential items include:
- A welding helmet with the appropriate lens shade.
- Flame-resistant gloves and clothing.
- Safety boots and welder’s caps for additional protection.
For both MIG and TIG welding, ensure proper ventilation and local exhaust to minimize exposure to fumes and gases. Regularly inspect your safety gear to ensure it’s in good condition and replace any worn-out items promptly. Remember that different welding positions may require specific safety considerations, so always adjust your approach accordingly.
Wrapping It Up
Choosing between MIG and TIG welding really comes down to what you need for your project. MIG welding is quick, easy to learn, and great for larger tasks or when you’re working with thicker materials. On the other hand, TIG welding gives you more precision and cleaner results, making it ideal for detailed or delicate work. Both methods have their strengths and weaknesses, so it’s all about figuring out what fits your goals best.
When considering TIG and MIG welding differences, remember that MIG excels in speed and ease of use, while TIG offers unparalleled precision and weld aesthetics. Your choice may depend on factors like material thickness, desired weld strength, and the level of welding control you need for your project.
Whether you’re a beginner or a seasoned pro, understanding these differences will help you make the right call. Happy welding!
Frequently Asked Questions
What is the main difference between MIG and TIG welding? MIG welding uses a continuously fed wire as both the electrode and filler material, while TIG welding uses a non-consumable tungsten electrode and may require a separate filler rod.
Which welding method is easier for beginners to learn? MIG welding is generally easier for beginners because it has a simpler process and requires less coordination than TIG welding.
What type of projects is MIG welding best suited for? MIG welding is ideal for larger projects that require speed and efficiency, such as construction work or automotive repairs.
Why is TIG welding considered more precise? TIG welding allows for greater control over the weld, making it ideal for projects that require fine details and clean, high-quality welds.
Is TIG welding more expensive than MIG welding? Yes, TIG welding equipment and the process itself tend to be more expensive due to the need for specialized tools and a slower welding speed.
What safety gear is needed for MIG and TIG welding? Both methods require safety gear like welding helmets, gloves, and protective clothing to shield against sparks, heat, and harmful UV rays.