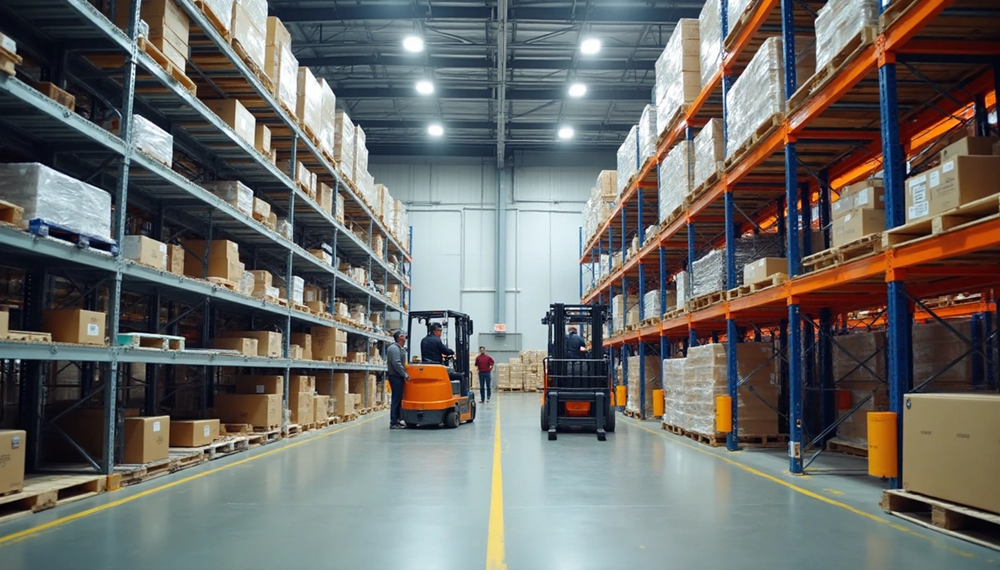
The rack vs shelf choice affects everything from storage capacity to your bottom line, though many people see them as interchangeable. Widespan shelves can hold up to 2,000 pounds per shelf. Racking systems, however, are built to support palletized products that weigh 1,000 pounds or more. This basic weight capacity difference marks just the start of what sets these storage solutions apart.
Storage solutions differ beyond simple names. Industry standards indicate that storage aids 30 inches deep or less are considered shelves, while deeper options fall under rack requirements. Shelving works best for lightweight items you can grab by hand. Racks support heavier loads and require equipment to access. Your choice between a rack vs shelf unit can streamline processes, maximize space usage, and keep your facility safe.
Rack vs shelf vs bay terms often mix people up, but picking the right one is vital. Light pallet racking outperforms even the strongest shelving units. Modern racking systems anchor permanently to floors or walls and need machines to load and unload. This shows their industrial-grade build quality. Smart storage choices do more than organize—they shape your operational costs and future profits.
Understanding the Core Differences
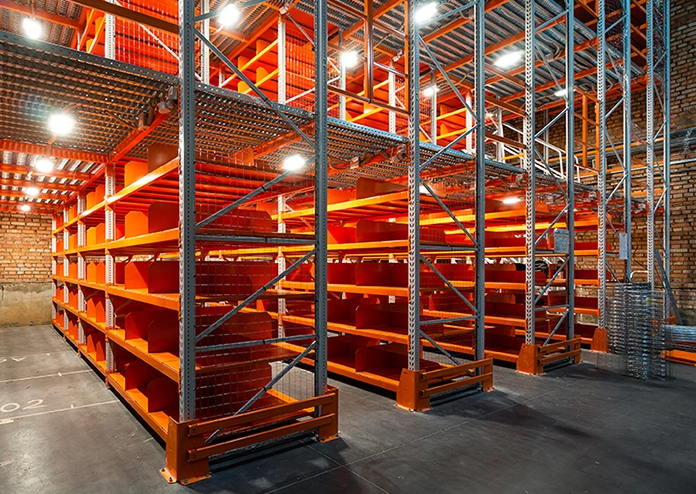
Racks and shelves have key differences that go beyond looks. These differences affect how people store and access materials in warehouses, retail spaces, and homes.
Weight Handling: Manual vs Machine Access
Storage solutions differ mainly in their access methods and weight capacity. Shelving units work best with items that staff can stock and retrieve by hand, which makes them perfect for smaller, lighter products. Rack systems handle heavy loads and require forklifts or specialized equipment for quick operation. This core difference shapes where each system works best. Staff can easily access inventory on shelves, while racks excel in high-volume warehousing where loads weigh more than 1,000 pounds per pallet.
Design Structure: Solid Deck vs Beam Support
The way these systems are built creates another major difference. Most shelves have solid decking surfaces that spread weight evenly across the platform. Boltless shelving shares features with racks, using vertical frames and shelf beams, but needs a decking surface for hand-loaded items under 1,000 pounds. Pallet racking uses vertical upright frames joined by horizontal beams that hold palletized loads. The beams move weight to the uprights and create an open structure that maximizes vertical space. Rack systems offer various decking options for non-palletized storage. Wire mesh can hold 2,200 to 3,650 pounds, perforated steel supports 3,000 pounds per section, and solid steel decking provides another option.
Shelf vs Rack vs Bay: Terminology Explained
Storage industry terms help make the right choice between shelves and racks. A “bay” means the space between two upright columns in a racking system. The “rack cell” describes one beam level’s space between two uprights, which usually fits two pallet positions. Single shelf racks offer flexible storage for items that don’t work well on pallets, such as smaller products or office supplies. The “beam” serves as the horizontal part that carries the load weight to the uprights. Each system serves a unique purpose – shelves focus on easy access and organization, while racks maximize weight capacity and space use.
Types of Shelving and Racking Systems
Warehouses and retailers can choose from several unique storage options that match their specific operational needs and storage requirements.
Steel, Wire, and Rivet Shelving Options
Steel shelving systems deliver affordable and durable solutions in various settings. Wire shelving stands out with better visibility, less dust buildup, and better air flow – perfect for food service and medical facilities. These units hold up to 800 pounds per shelf and carry NSF certification for sanitary environments. Rivet shelving, also called boltless shelving, uses a unique snap-in design for quick tool-free assembly. A single rivet unit handles up to 350 pounds, while double rivet configurations support between 1,600 and 2,000 pounds for units 48 inches wide or less.
Pallet, Pushback, and Flow Racking Explained
Pallet racking systems store materials on multiple levels and use vertical space through horizontal rows. Pushback rack systems work on a Last-In-First-Out (LIFO) principle and support up to six pallets deep. New pallets push existing inventory back along inclined rails. Pallet flow racks operate on a First-In-First-Out (FIFO) basis and work best for perishable goods that need rotation. These systems handle up to 20 pallets deep and use braking mechanisms to control pallet movement. Selective pallet racks offer 100% load accessibility, while drive-in racks provide high-density storage with shared entry points.
Single Shelf Rack: When It Makes Sense
Single shelf racks shine in spaces that need access to items under existing pallet racking or in tight areas. These floor units make it easy to reach difficult items and feature structural steel construction for lasting durability. Roll-out floor shelf options handle up to 2,000 pounds and boost space usage while keeping operators safe. Industrial, warehouse, and manufacturing settings benefit from these specialized racks where standard shelving falls short.
Custom Configurations for Hybrid Storage
Multi-tier racking creates adaptable storage solutions by placing aisle levels at different heights connected by stairs. This setup maximizes vertical space and adapts to different storage needs. Hybrid systems combine cantilever racks for long items with standard shelving for smaller products. Mobile shelving systems on movable bases offer flexibility, especially in spaces with limited room.
Cost Breakdown and Long-Term Value
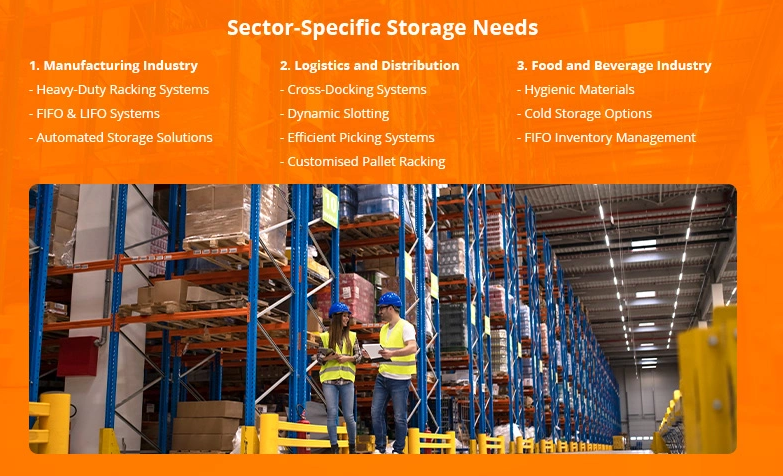
Businesses base their storage system investments on what fits their budget. A good grasp of what shelving and racking solutions cost helps companies make smart choices for both now and later.
Original Setup Costs: Shelving vs Racking
These storage options come with very different price tags. Shelving systems are budget-friendly to start with because they’re easier to build and set up. To cite an instance, boltless shelving keeps costs down since workers can put it together quickly. Rack systems, on the other hand, need more money upfront due to their resilient construction and engineering needs. Heavy-duty steel makes racks get pricey, ranging from USD 300-1,500+ per bay, while shelving units cost USD 100-500 each. Racks also need special equipment or professional installers, which adds to the initial expense.
Maintenance and Durability Over Time
Racks might cost more at first, but they’re worth it in the long run if you take care of them. Good maintenance stops expensive fixes and makes equipment last longer. Both systems need checks for loose bolts, bent parts, and wear and tear. Rack systems need more thorough inspections because they handle industrial loads. This means checking bolt tightness and adding guards like ballards and rails to protect racks from forklifts. These safety steps help avoid replacing expensive parts later.
Space Utilization: Which Saves More Per Square Foot?
Storage solutions’ real value comes down to how well they use space. Racks might cost more upfront, but give better value per square foot by using height better. Warehouse managers often find they use just 22-35% of their vertical space before switching to proper racking. Better rack layouts can cut forklift travel time by 15-25%, saving about USD 4,200 yearly per lift.
Accessory Costs: Bins, Dividers, and Add-ons
Extra parts play a big role in total costs. Bin dividers split storage units into smaller spaces for tiny parts, which makes the most of available space. These add-ons’ prices change based on what they’re made of (plastic, metal, or custom materials) and how they’re set up. Bin cups also create spaces within shelves to sort small items like nuts, screws, and bolts. These extras improve organization but need to be part of your long-term budget plan.
Choosing the Right System for Your Needs
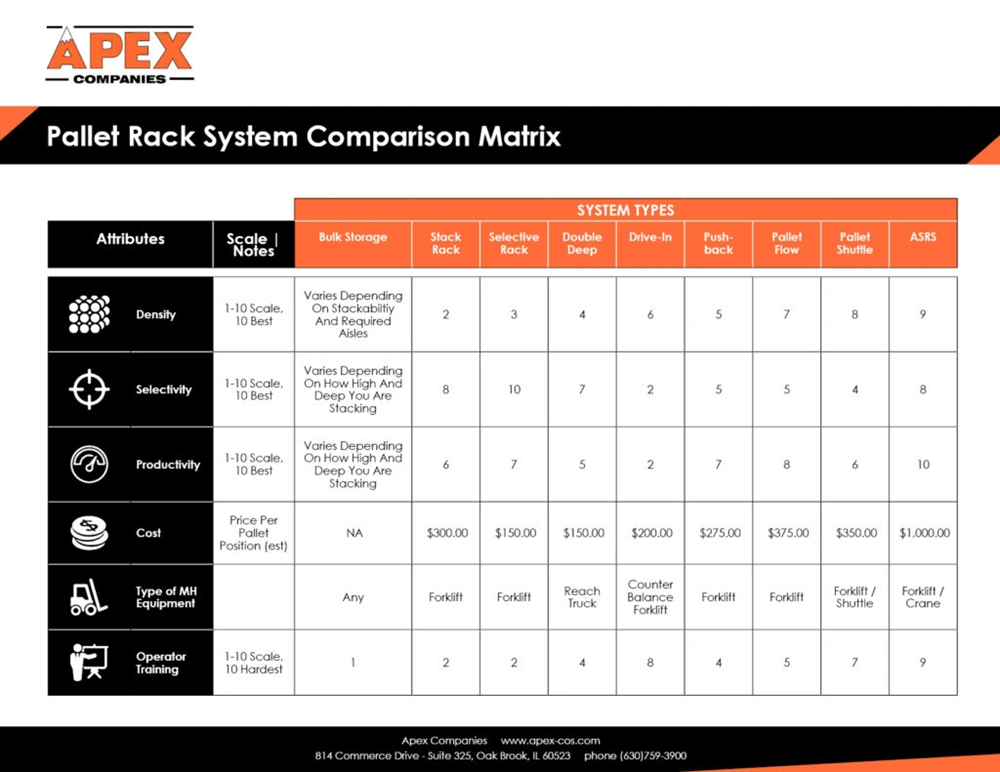
Choosing between rack and shelf storage systems means you just need to evaluate your operational setup and requirements. Your storage needs, item types, and business goals will determine the right choice.
Warehouse vs Retail vs Home Use
Each environment just needs its storage solution. Industrial warehouses use racking systems to store palletized goods and handle high-capacity storage. Retail spaces work better with shelving that lets customers see products easily and makes shopping more enjoyable. People at home usually go for shelving systems because they’re versatile and take up less space. Distribution centers work quite differently from retail warehouses. They focus on moving products quickly through receiving, storage, and shipping areas. Retail spaces put customer experience first with smart product placement.
When to Use a Rack vs Shelf Unit
Your inventory type should guide your choice between rack and shelf units. Shelving works best for lighter items you access often, organizing various products, or creating multipurpose storage. Racking systems make more sense for palletized materials, heavy bulk items, or making the most of vertical space. The rule is simple – if you’re using a forklift, you’ll want racking. Manual handling calls for shelving.
Scalability and Future Expansion
Growth planning is crucial for storage systems. Flexible solutions help businesses adapt without costly upgrades. You can scale in two ways: vertical scaling adds more storage to what you have, while horizontal scaling means adding new storage units. Vertical expansion stays within fixed controllers. Horizontal expansion boosts both capacity and performance – perfect for growing operations with changing inventory needs.
Safety and Compliance Considerations
Each system comes with its own safety rules. Rack installations just need permanent floor anchoring to stay stable and safe, especially given their height and weight capacity. Following industry standards like ANSI MH16.1 for selective racks and ANSI MH28.2 for boltless shelving will give a proper setup and operation. Regular checks help spot weak spots, prevent overloading, and keep operations safe. Ignoring these rules can lead to workplace injuries, damaged products, and legal issues.
Comparison Table
Feature | Shelving | Racking |
---|---|---|
Weight Capacity | Up to 2,000 lbs per shelf | 1,000+ lbs per pallet |
Depth Specification | 30 inches or less | Greater than 30 inches |
Access Method | Manual, available by hand | Machine-operated (forklifts) |
Installation | Simple assembly, often boltless | Permanently anchored to floors/walls |
Main Use | Lightweight items, frequent access needs | Palletized products, heavy loads |
Original Cost | $100-500 per unit | $300-1,500+ per bay |
Maintenance Requirements | Simple inspections | Rigorous checks, retorquing hardware |
Loading Method | Hand-loaded items under 1,000 lbs | Typically loaded by machines |
Structure Type | Solid decking surfaces | Vertical frames with horizontal beams |
Best Environment | Retail, small storage, office supplies | Warehouses, industrial settings |
Conclusion
The choice between racks and shelves depends on your business needs. There’s no one-size-fits-all solution here. Weight capacity is the main difference – shelves can hold up to 2,000 pounds each, while racks handle palletized loads that exceed 1,000 pounds. This affects how you use them. Shelves work best when staff need to access lighter items by hand. Racks are a better fit for heavy goods that need forklift handling.
Money matters show a clear trade-off between these storage options. Shelves cost less upfront, ranging from $100-500 per unit. Racks cost more at $300-1,500+ per bay. But racks that are well-kept end up offering better long-term value by maximizing vertical space. Companies often find they used only 22-35% of their vertical space before switching to proper racking solutions.
These systems have different safety needs too. Racks must be anchored to the floor permanently and meet ANSI MH16.1 standards. Shelves follow simpler rules. Both options need regular upkeep, but racks need more thorough checks because of their industrial use and heavier loads.
Your environment should guide the final choice. Warehouses and distribution centers work better with racks designed for product movement and palletized storage. Retail spaces and offices prefer shelves because they make products visible and easy to reach. The choice between racks and shelves is more than just picking storage – it’s a strategic decision that shapes how well you operate, use space, and manage costs.
Key Takeaways
Understanding the fundamental differences between racks and shelves can significantly impact your storage costs and operational efficiency:
• Weight capacity determines choice: Shelving handles up to 2,000 lbs per shelf for manual access, while racking supports 1,000+ lbs requiring forklift operation.
• Initial costs favor shelving: Shelving units cost $100-500 versus $300-1,500+ for racking bays, but racking delivers better long-term value through vertical space maximization.
• Space utilization drives ROI: Most facilities use only 22-35% of vertical space before implementing proper racking, making it more cost-effective per square foot.
• Application context matters most: Choose shelving for retail/office environments with frequent manual access needs; select racking for warehouses handling palletized goods.
• Safety requirements differ significantly: Racking demands permanent floor anchoring and rigorous maintenance, while shelving follows simpler installation and inspection protocols.
The decision between racks and shelves isn’t just about storage—it’s a strategic investment that affects your operational efficiency, space utilization, and long-term profitability. Consider your specific weight requirements, access methods, and growth plans when making this crucial choice.
FAQs
Q1. What’s the main difference between racks and shelves? The primary difference is weight capacity. Shelves typically support up to 2,000 pounds per shelf and are designed for manual access, while racks can handle palletized loads exceeding 1,000 pounds and often require machine operation.
Q2. Which storage solution is more cost-effective in the long run? While shelving has lower initial costs, racking systems often provide better long-term value through maximized vertical space utilization. Racking can help businesses use up to 78% more of their available vertical space compared to traditional shelving.
Q3. How do I choose between racks and shelves for my business? Consider your storage needs, item characteristics, and operational environment. Choose shelving for lighter items requiring frequent manual access, and opt for racking when handling heavy palletized materials or maximizing vertical space in warehouses.
Q4. Are there different safety requirements for racks and shelves? Yes, safety requirements differ significantly. Racking installations typically require permanent floor anchoring and adherence to specific industry standards, while shelving follows less stringent protocols. Both systems need regular maintenance, but racking demands more rigorous inspections.
Q5. Can I use a combination of racks and shelves in my storage setup? Absolutely. Many businesses benefit from hybrid storage solutions that combine racks and shelves to accommodate diverse inventory needs. This approach allows for efficient storage of both palletized goods and smaller, manually accessed items within the same facility.